
Evofosfamide, HAP-302 , TH-302
![]() | |
NAMES | |
---|---|
IUPAC name
(1-Methyl-2-nitro-1H-imidazol-5-yl)methyl N,N’-bis(2-bromoethyl)phosphorodiamidate
| |
Other names
TH-302; HAP-302
| |
IDENTIFIERS | |
918633-87-1 ![]() | |
ChemSpider | 10157061 ![]() |
Jmol-3D images | Image |
PubChem | 11984561 |
PROPERTIES | |
C9H16Br2N5O4P | |
Molar mass | 449.04 g·mol−1 |
6 to 7 g/l |
TH-302 is a nitroimidazole-linked prodrug of a brominated derivative of an isophosphoramide mustard previously used in cancer drugs
evofosfamide (first disclosed in WO2007002931), useful for treating cancer.
Threshold Pharmaceuticals and licensee Merck Serono are codeveloping evofosfamide, the lead in a series of topoisomerase II-inhibiting hypoxia-activated prodrugs and a 2-nitroimidazole-triggered bromo analog of ifosfamide, for treating cancer, primarily soft tissue sarcoma and pancreatic cancer (phase 3 clinical, as of April 2015).
In November 2014, the FDA granted Fast Track designation to the drug for the treatment of previously untreated patients with metastatic or locally advanced unresectable soft tissue sarcoma.
Evofosfamide (INN,[1] USAN;[2] formerly known as TH-302) is an investigational hypoxia-activated prodrug that is in clinical development for cancer treatment. The prodrug is activated only at very low levels of oxygen (hypoxia). Such levels are common in human solid tumors, a phenomenon known as tumor hypoxia.[3]
Evofosfamide is being evaluated in clinical trials for the treatment of multiple tumor types as a monotherapy and in combination with chemotherapeutic agents and other targeted cancer drugs
Discovered at Threshold, TH-302 is a hypoxia-activated prodrug (HAP) designed to exploit low oxygen levels in hypoxic tumor regions. Therapeutics that specifically target resistant hypoxic zones could provide significant additional antitumor activity and clinical benefit over current chemotherapeutic and radiation therapies.
Discovered at Threshold, TH-302 is a hypoxia-activated prodrug (HAP) designed to exploit low oxygen levels in hypoxic tumor regions. Therapeutics that specifically target resistant hypoxic zones could provide significant additional antitumor activity and clinical benefit over current chemotherapeutic and radiation therapies.
Evofosfamide (TH-302) was developed by Threshold Pharmaceuticals Inc. (Threshold).[4] The company is located in South San Francisco, CA, USA.
In 2012, Threshold signed a global license and co-development agreement for evofosfamide with Merck KGaA, Darmstadt, Germany, which includes an option for Threshold to co-commercialize eofosfamide in the United States. Threshold is responsible for the development of evofosfamide in the soft tissue sarcoma indication in the United States. In all other cancer indications, Threshold and Merck KGaA are developing evofosfamide together.[5] From 2012 to 2013, Merck KGaA paid 110 million US$ for upfront payment and milestone payments to Threshold. Additionally, Merck KGaA covers 70% of all evofosfamide development expenses.[6]
Discovered at Threshold, TH-302 is a hypoxia-activated prodrug (HAP) designed to exploit low oxygen levels in hypoxic tumor regions. Therapeutics that specifically target resistant hypoxic zones could provide significant additional antitumor activity and clinical benefit over current chemotherapeutic and radiation therapies.
Discovered at Threshold, TH-302 is a hypoxia-activated prodrug (HAP) designed to exploit low oxygen levels in hypoxic tumor regions. Therapeutics that specifically target resistant hypoxic zones could provide significant additional antitumor activity and clinical benefit over current chemotherapeutic and radiation therapies.
History
DATE | EVENT |
---|---|
Jun 2005 | Threshold files evofosfamide (TH-302) patent applications in the U.S.[49] |
Jun 2006 | Threshold files a evofosfamide (TH-302) patent application in the EU and in Japan[50] |
Sep 2011 | Threshold starts a Phase 3 trial (TH-CR-406) of evofosfamide in combination withdoxorubicin in patients with soft tissue sarcoma |
Feb 2012 | Threshold signs an agreement with Merck KGaA to co-develop evofosfamide |
Apr 2012 | A Phase 2b trial (TH-CR-404) of evofosfamide in combination with gemcitabine in patients with pancreatic cancer meets primary endpoint |
SEE
WO2007002931
Example 8
Synthesis of Compounds 25, 26 [0380] To a solution of 2-bromoethylammmonium bromide (19.4 g) in DCM (90 mL) at – 1O0C was added a solution OfPOCl3 (2.3 mL) in DCM (4 mL) followed by addition of a solution of TEA (14.1 mL) in DCM (25 mL). The reaction mixture was filtered, the filtrate concentrated to ca. 30% of the original volume and filtered. The residue was washed with DCM (3×25 mL) and the combined DCM portions concentrated to yield a solid to which a mixture of THF (6 mL) and water (8 mL) was added. THF was removed in a rotary evaporator, the resulting solution chilled overnight in a fridge. The precipitate obtained was filtered, washed with water (10 mL) and ether (30 mL), and dryed in vacuo to yield 2.1 g of:
Isophosphoramide mustard
can be synthesized employing the method provided in Example 8, substituting 2- bromoethylammmonium bromide with 2-chloroethylammmonium chloride. Synthesis of Isophosphoramide mustard has been described (see for example Wiessler et al., supra).
The phosphoramidate alkylator toxin:
was transformed into compounds 24 and 25, employing the method provided in Example 6 and the appropriate Trigger-OH.
Example 25
Synthesis of l-N-methyl-2-nitroimidazole-5-carboxylis acid
A suspension of the nitro ester (39.2 g, 196.9 rnmol) in IN NaOH (600 mL) and water (200 mL) was stirred at rt for about 20 h to give a clear light brown solution. The pH of the reaction mixture was adjusted to about 1 by addition of cone. HCl and the reaction mixture extracted with EA (5 x 150 mL). The combined ethyl acetate layers were dried over MgS O4 and concentrated to yield l-N-methyl-2-nitroimidazole-5-carboxylis acid (“nitro acid”) as a light brown solid (32.2 g, 95%). Example 26
Synthesis of l-N-methyl-2-nitroimidazole-5-carboxylis acid
A mixture of the nitro acid (30.82 g, 180.23 mmol) and triethylamine (140 niL, 285 mmol) in anhydrous THF (360 mL) was stirred while the reaction mixture was cooled in a dry ice-acetonitrile bath (temperature < -20 0C). Isobutyl chloroformate (37.8 mL, 288 mmol) was added drop wise to this cooled reaction mixture during a period of 10 min and stirred for 1 h followed by the addition of sodium borohydride (36 g, 947 mmol) and dropwise addition of water during a period of 1 h while maintaining a temperature around or less than O0C. The reaction mixture was warmed up to O0C. The solid was filtered off and washed with THF. The combined THF portions were evaporated to yield l-N-methyl-2- nitroimidazole-5-methanol as an orange solid (25 g) which was recrystallized from ethyl acetate.
……………………………………….
WO-2015051921

EXAMPLE 1

1
N-Formylsarcosine ethyl ester 1 (1 ,85 kg) was dissolved in toluene (3,9 kg) and ethyl formate (3,28 kg) and cooled to 10 °C. A 20 wt-% solution of potassium tert-butoxide (1 ,84 kg) in tetrahydrofuran (7,4 kg) was added and stirring was continued for 3h. The reaction mixture was extracted 2x with a solution of sodium chloride in water (10 wt-%) and the combined water extracts were washed lx with toluene.
Aqueous hydrogen chloride (25% wt-%; 5,62 kg) was added to the aqueous solution, followed by ethylene glycol (2,36 kg). The reaction mixture was heated to 55-60 °C for lh before only the organic solvent residues were distilled off under vacuum.
Aqueous Cyanamide (50 wt-%, 2,16 kg) was then added at 20 °C, followed by sodium acetate (3,04 kg). The resulting reaction mixture was heated to 85-90 °C for 2h and cooled to 0-5 °C before a pH of ~ 8-9 was adjusted via addition of aqueous sodium hydroxide (32% wt-%; 4,1 kg). Compound 3 (1,66 kg; 75%) was isolated after filtration and washing with water.
Ή-NMR (400 MHz, d6-DMSO): δ= 1,24 (3H, t, J= 7,1 Hz); 3,53 (3H, s); 4,16 (2H, q, J= 7,0 Hz) ; 6,15 (s, 2 H); 7,28 (s, 1H).
HPLC (Rt = 7,7 min): 97,9% (a/a).
REFERENCES
1
- WHO Drug Information; Recommended INN: List 73
- 2
- Adopted Names of the United States Adopted Names Council
- 3
- Duan J; Jiao, H; Kaizerman, J; Stanton, T; Evans, JW; Lan, L; Lorente, G; Banica, M et al. (2008). “Potent and Highly Selective Hypoxia-Activated Achiral Phosphoramidate Mustards as Anticancer Drugs”. J. Med. Chem. 51 (8): 2412–20. doi:10.1021/jm701028q. PMID 18257544.
- 4
- Website of Threshold Pharmaceuticals Inc.
- 5
- Threshold Pharmaceuticals and Merck KGaA Announce Global Agreement to Co-Develop and Commercialize Phase 3 Hypoxia-Targeted Drug TH-302 – Press release from 3 February 2012
- 6
DHAKA BANGLADESH



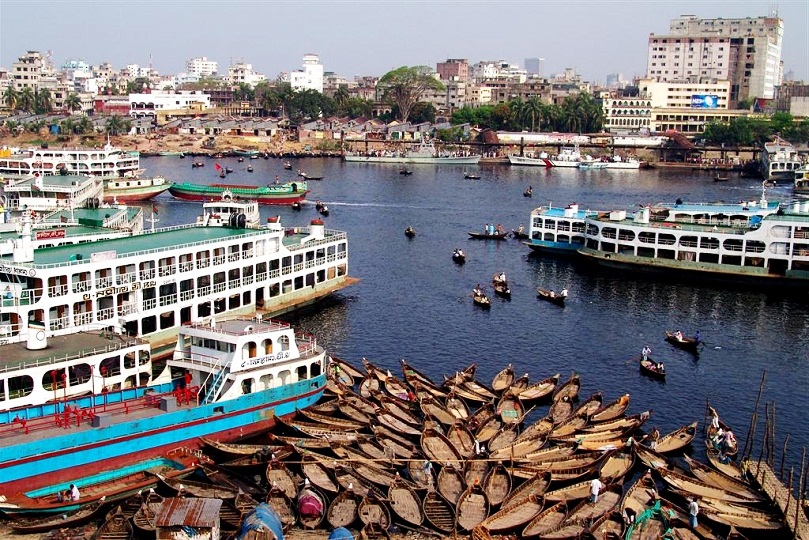

Steamers and ferries in Sadarghat Port



